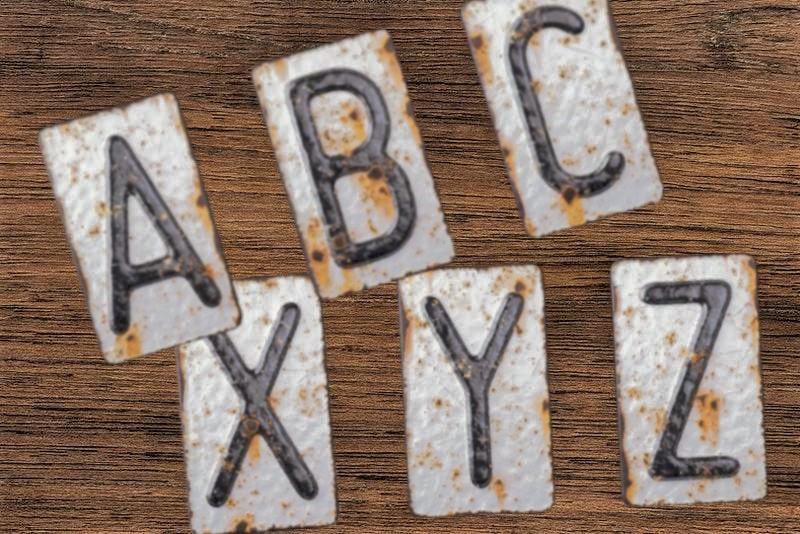
05 Mar Combination of ABC / XYZ strategies in SAP
Reading time: 2 min
Keywords: ABC/XYZ strategies in SAP, Inventory management optimization
Authors: Dimitrios Megkas, Elpida Mezili
Inventory management optimization can be achieved by combining the well-known ABC and XYZ strategies. For example, we could have an ABC sales/code analysis and an XYZ demand/code analysis. By combining these two, we can derive a sales analysis of demand fluctuations. From the size of the share of value and the size of the rate of change of receivables, the component of the forecast value is derived.
By classifying the materials based on the above component, we would lead to useful conclusions about the movement of the codes and the corresponding maintained inventory. Therefore, in materials with a low savings margin, we could have full automation and the planner could focus on materials with a high savings margin. In between, there could be medium-margin materials, for which there would be, in principle, automation in planning, but with an information mechanism for special cases where deviations tend to inflate.
This process is obviously dynamic and it should be considered as a fact that a material will change classification in the ABC / XYZ analysis. The determining factor in this is the so-called product life cycle, which is divided into the following phases:
- Introduction
- Development
- Maturity
- Saturation
- Decline
So, depending on what stage of the life cycle of a material is, the classification will provide a different result. There is even the possibility of classification at different levels, such as country, product category, installation. There again, depending on the classification we want, the results will differ.
A successful introduction of ABC / XYZ analysis requires an optimization task. This project includes the following main steps:
- Analysis of basic data and procedures. At this stage and with the help of tools provided by the system, the evaluation of the quality of the basic file data and any weaknesses in the process/communication within the organization is performed.
- MRP training. Problems often arise when there is a lack of documentation/training and those responsible for planning the materials do not know all the features of the system. In this step, therefore, any weak points and specific knowledge gaps are identified, and the necessary actions are performed to overcome/cover them.
- Classification and creation of rules set. Once all the preliminary checks have been done, the procedures have been analyzed and the necessary knowledge has been secured, a set of rules for material planning is created. The materials are classified in a specific order and an ABC / XYZ matrix is drawn up.
- Data transfer and continuous optimization. At the end of the process, the MRP parameters of the materials are updated in bulk, based on a specific plan and rules. Then, at regular intervals, reclassification is performed and indicators of material planning quality are used.